No more manual or messy powdering for your PROFESSIONAL DTFcesses! With this compact and well designed Vastex, DTF powder is evenly distributed to your DTF sheets via the push of a lever, and excess powder is evenly and automatically removed at the push of a button. Powder adheres only to your printed areas, and excess powder is easy to recirculate for additional uses.
Holds the following DTF film sizes (adjustable):
- A4 sheets
- A3 sheets
- A3+ sheets
- 16 in x 20 in sheets
BENEFITS:
- Accepts DTF film up to and including 16 in x 20 in sizes
- Compact Desktop footprint
- Easy operation and zero maintenance
- Beginner Friendly
- Compact and well designed
- Applies an even distribution of powder
- Adjustable timer
- Sealed for mess-free operation
- Interchangeable cartridges for quick and clean refills
- Improved DTF workflow
Available Options:
Vastex PTF-100 | Vastex PTF-100 with Stand | Vastex PTF-100 with Stand and Drawers | Vastex PTF-100 with Stand and D100 Conveyor Dryer |
---|
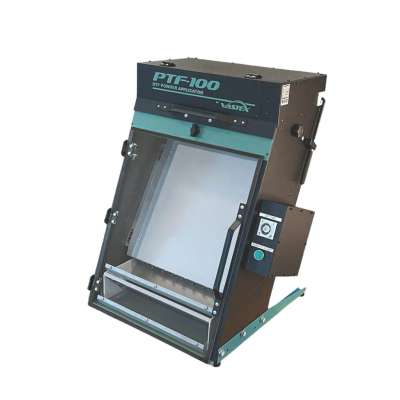 | 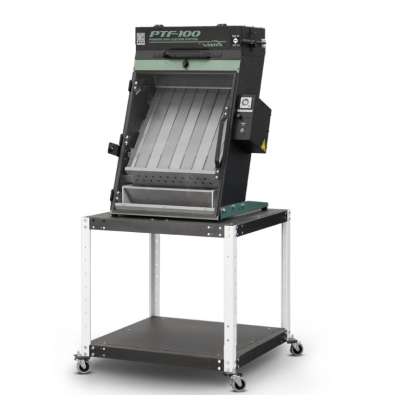 | 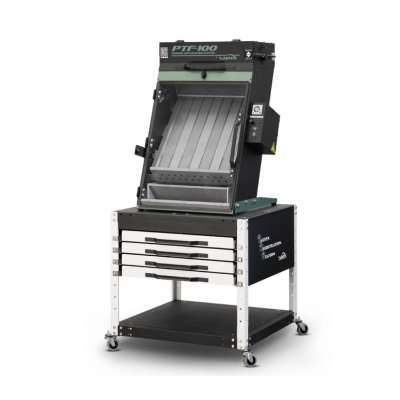 | 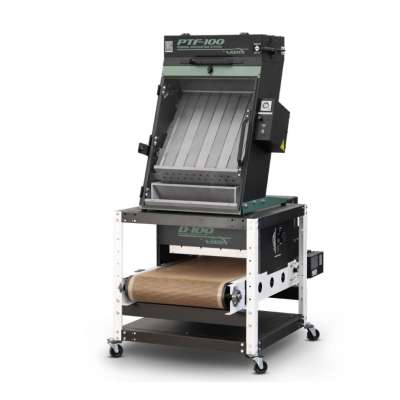 |
| - Vastex PTF-100
- Rolling Stand
| - Vastex PTF-100
- Rolling Stand
- 4 Drawer Accessory Kit
| - Vastex PTF-100
- Rolling Stand
- D100 Conveyor Dryer
|
$2,089.99 | $2,349.99 view item | $2,999.99 view item | $5,299.99 view item |
ECONOMICAL
Interchangeable cartridges minimize waste, offers quick and clean refills.
VERSATILE
Fits up to 16 x 20 in. films
CONSISTENT
Both the angle of powder deflection and timer are adjustable for repeatable results
STURDY
Powder-coated stainless steel case and polycarbonate door for years of use
DUST-FREE
Sealed for mess-free operation
The PTF-100 Powder-To-Film system, also known as a Powder Shaker, uniformly coats DTF films with adhesive powder, improving DTF printing performance and operator safety. Instead of hand-coating DTF films in open plastic containers that expose shop personnel to adhesive dust and require operator time and attention to obtain reliable results, the PTF-100 system provides uniform coverage without dusting and spillage, reducing waste and freeing staff to optimize production time.
Purpose-built for DTF printing, the tabletop unit consists of a steel case on a stand, with a clear polycarbonate door set at an angle. It comes with two identical cartridges, each of which can hold approximately 3 lbs (1.4 kg) of adhesive powder. It has a rear mounted exhaust designed to collect adhesive dust particles and create a "negative pressure" condition within the cabinet. The film tray is suspended on special rubber hangers that isolate it from the intense vibration applied to remove excess powder from the film.
To operate, a filled cartridge is inserted at the top of the unit, and an empty cartridge at the bottom. An operator positions the wet DTF printed film on the application tray, print side up. Once the polycarbonate door is closed tightly, the operator adjusts the position of the powder deflector to accommodate the size of film being coated.
An adjustable timer allows the operator to adjust the duration of vibration, achieving repeatable results. To initiate a cycle, the user pushes up a lever to release the desired amount of powder, then pulls the same lever down to start the timer vibration. The top cartridge releases adhesive powder, which rains down on the film, ensuring complete and even coverage. When empty, the upper cartridge can be switched quickly and cleanly with the lower cartridge containing all excess powder, reducing exposure while eliminating waste and allowing continuous production until refilling is needed. Made in the USA, the PTF-100 can accommodate film sizes up to 16 x 20 in. (406 to 508 mm).
The PTF-100 Powder-To-Film system pairs well with a Vastex D-100 or D-1000 tabletop conveyor dryer equipped with rear mounted powered exhaust hood to vent glycol fumes from the shop environment. DTF also offers heat presses and sturdy mobile utility stands that can accommodate most DTF equipment to optimize the shop floor layout.